2024 EUROPEAN
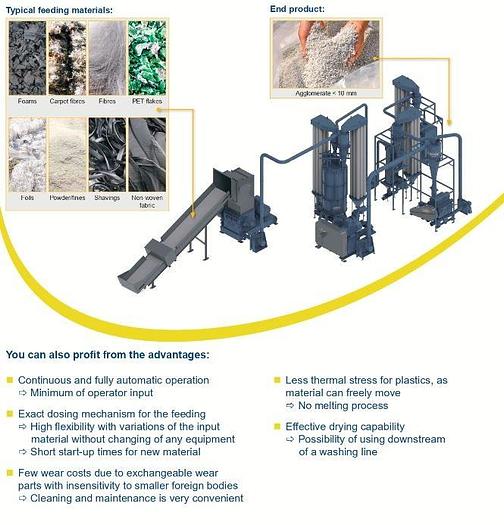
2024 EUROPEAN
Contact us for price
Description
FULLY AUTOMATIC AGGLOMERATING LINE FOR PLASTIC MATERIALS
Including:
HEAVY DUTY GRANULATOR
Cutting chamber opening appr. 720 x 980 mm
Rotor diameter 600 mm
Rotor length 980 mm
Rotor knives 4x2 D2 chrome nickel tool steel
Stator knives 2x1
Drive 75 kW
Feed hopper
In sturdy welded steel design with strengthening ribs on the surface of the hopper. Fitted with heavy duty solid plastic safety flaps and / or curtains to prevent material flyback.
Housing design
Centrally hinged two-piece welded steel design, upper and lower housing units meet at an inclined angle. Both bed knives are mounted to opposite sides of the dividing surface.
Opening and closing of the housing by a hand winch.
Rotor design
Open 4 x 2 knives rotor: No threads tapped into the rotor, knives are fastened with hexagonal bolts and knife mounting plates. Optimal knife seat with back stops on each rotor cross member. The rotor knives have adjustment screws at the rear.
Rotor bearing:
Self-aligning roller bearings in pillow block bearing housings, completely outside and separated from the grinding chamber. Both bearings with regreasing possibility.
Base frame
Flat welded steel design to take the granulator with the drive motor (on tension rails). The frame is supplied with anti-vibration pads.
Pulleys
The granulator pulley is designed as a solid flywheel with SPC profiles.
Drive motor
75 kW three-phase motor, type B3 protection IP 55, 400 V,
50 Hz, appr.1500 rpm, heavy duty bearings, TEFC.
Safety devices
Integrated run down safety devices prevent access to the unit until the rotor has reached a standstill. Seals according to CE standards.
Pneumatic Discharge and Transport System
Customer to feed his pre-shredded material to the storage silo.
material blower with 11 kW drive motor,
connecting pipework,
a cyclone separator with mounting frame for forwarding the material to the silo.
Extract air hood and filter bags.
Agglomerating unit
Consisting of:
1 Storage silo (4 m3) with feeding screw
Filling volume: approx. 4 m³
Silo height (cylinder): approx. 2.800 mm
Silo diameter: approx. 1.400 mm
Material: mild steel
Drive discharge scraper/agitator: approx. 5,5 kW
Drive discharge screw silo: approx. 2,2 kW
Drive feeding screw compactor: approx. 22 kW
Drive screw sliding (maintenance): approx. 0,75 kW
Round design to avoid bridging of difficult flowing materials.
Continuous and metered discharge of the material out of the storage silo into a discharge screw by a discharge scraper The compactor feeding screw is continuously adjustable and conveys the material through the center of the stator disc into the working zone. Both screws are controlled via frequency converters.
The silo is equipped with level indicators and a maintenance door with inspection window.
Advantage: Different bulk densities don’t require adjustment / replacement of the conveying screw.
For maintenance purposes the compactor feeding screw mounted on slide bars can be moved manually thus ensuring an optimum access to the compactor discs.
DISK TYPE AGGLOMERATOR
The silo discharge, the screw feeding device and the compacting unit are one process system.
The feeding screw force feeds the material controlled by the current consumption of the compacting unit into the compacting discs. The compacting takes place in the compactor unit between the rotary and stationary compacting discs.
The gap between the discs is automatically adjusted during operation.
For opening the compactor housing. The feeding screw is moved manually to the back. This allows excellent access for cleaning and maintenance work.
Housing:
In welded steel design
Compacting discs:
Installed in the housing, gap clearance of discs adjustable via remote control, both discs are cooled with water.
Disc diameter 700 mm.
Bearing of rotating disc:
Roller bearings in flange bearing housing, bearing sealing through radial shaft sealings
Drive:
V-belt drive, 250 kW motor, A/C current, type B3, protection IP 55, approx. 1.500 rpm, 400 V, 50 Hz
Drive oil circulation: approx. 0,18 kW
Drive disc adjustment: approx. 1,5 kW
Support:
Profile steel with belt-guard and motor rails.
1 Conveying system
Connecting pipework from compactor to the central blower
15 kW, connecting pipework to the cyclone separator II with feed hopper to the granulator. Exhaust air to be conveyed to the outside.
Common base frame for compactor, drive and feeding device Advantage: no need for a separate isolated foundation
HOT MELT GRANULATOR
Cutting chamber opening: approx. 780 x 980 mm
Rotor diameter: 600 mm
Rotor length: 980 mm
Rotor knives: 7x2
Stator knives: 2x1
Drive: 75 kW
Knife quality:
All knives are manufactured from high quality chrome nickel tool steel.
Cutting geometry:
Double cross cutting action, i.e. the rotor knives are mounted at the same inclined angle but opposed to each other.
Knife adjustment:
this is carried out outside of the granulator in a jig supplied with the machine.
Rotor bearings:
self aligning roller bearings in steel pillow blocks completely outside and separate from the grinding chamber. Closed design with permanent lubrication.
Housing design:
centrally hinged two piece welded steel design - upper and lower housing units meet at an inclined angle. Both bed knives are mounted to opposite sides of the dividing surface.
Screen:
Easy screen change
Safety devices:
integrated run down safety devices prevent access to the unit until the rotor has reached a stand still. Seal according to the EC safety standards.
Drive:
75 kW A/C motor, type B3, protection IP 55, 400 V, 50 Hz, 1500 rpm.
Intensive cooling system
Injection of water mist into the grinder for cooling the agglomerate
Conveying system and recycling system for fines
Conveying system
For the discharge of the ground material.
Consisting of:
An 11 kW blower,
connecting pipework,
cyclone separator IV
single discharge nozzle,
support frame for the cyclone.
1 Recycling system for fines and for cooling
For the separation of fines and dust.
Consisting of:
Material infeed via rotary valve, approx. 1,1 kW, feed back of fines into the silo via rotary valve, approx. 1,1 kW
connecting pipework, fines separator and cooling unit designed as zig zag channel; in counter direction to the flow of the agglomerate, an air stream is sucked through the zig zag channel to take out the fines and for cooling the material. Including blower approx. 7,5 kW, 45 m³ air/min. The fines are returned to the storage silo.
Material Transport System with BigBag Station
Conveying system for big bag filling,
material blower with 11 kW drive motor,
connecting pipework, a cyclone separator with mounting frame, complete with twin big bag filling nozzles and an extract air hood with hanging filter bags.
Full level indicator and electro-pneumatic diverter valve
OPTION
1 full level indicator for each big bag (With optical or soiund alarm when message “full big bag” is issued)
1 electro-pneumatic diverter valve
The full level indicator detects when the big bag is full and transmits an electrical signal via the control cabinet to the diverter valve which then automatically switches over to the empty big bag. At the same time, a signal (option: optically or acoustically) is released which alerts the operating personnel. If the big bag is not exchanged after a time to be determined (in the control cabinet) and confirmed, the plant closes down automatically beginning at the front.
Service platform
Small service platform for easy hook in of big bags,
Recommendable for big bags higher than 1800 mm,
2 service platforms on 2 sides of the big bag station.
(Optional 3rd platform on the back side)
Electrical control with PLC control type S7-1500
The control cabinet contains all necessary protection devices, relays and fuses to operate the complete system.
Visualization with Siemens Touch Panel HMI 7“.
All drives can be controlled from the touch panel. Additional HMI units can be supplied against surcharge.
Operating conditions including motor failures are represented by symbols.
The operating mode is pre-selected via the touch panel.
1. Manual - Automatic operation / 2. Service mode
Manual: The drives can only be switched on successively according to the enabling sequence. When switching off, successive drives of the quoted plant are also switched off.
Automatic: The drives of the plant are switched on / off successively dependent on time and according to the enabling sequence.
Service: All drives can be switched on / off at will without enabling sequence.
A load interrupter switch (main switch) separates e. g. for maintenance work the plant from the network supply.
Control voltage for field devices (actuators and sensors) is 24V DC.
The compacting process is fully automatically controlled including automatic adjustment of the feeding device and the gap between the discs.
Recording of the operating parameters of the system (e.g. current, temperature, fill levels, speeds etc.).
The electrical control unit meets the relevant up to date EC directives.
Specifications
Manufacturer | EUROPEAN |
Year | 2024 |
Condition | New |
Stock Number | GE960 |